Here are some things that I need to check:
V_B - high side floating voltage should be 13- 20 V with reference to V_Sat no load it is 14.6 -good, however at load it drops to as low as 9V
check if this is at load or at low speed (done by putting 20% duty cycle on high side - 10% duty cycle on middle)
still 14.6V at 100rpm (measured by contact on tacho)
using 10% duty cycle now, and loading with the eddy current brake, I am now down to 74rpm or about 1.25 hz so I am somewhere close to operating conditions.
V_B is still at 14.5 V so I should be okay.
Now I need to understand what I am reading across the shunt resistor. For this I have connected V_s to the ground of the oscilloscope and V+ to the signal of the oscilloscope.
this is giving me garbage with a signals that is over 5V.
THE 10K NOISE IS ANNOYING ME - TIME TO CHANGE TO 20Kthis can be done by changing the "PWM_period" and the "on time" in the simlink program
still have a very annoying high pitched sound - maybe need higher than 20k. it also seems that I did not change it to 10% duty cycle before as now it is running at 30rpm (or 0.5hz).
back to the voltage accross the shunt resistor.this time I have added wires directly onto each end of the shunt resistor to be sure that I know what I am measuring.
the images below show the voltage accress the shunt resistor (in red) and the reading taken current clamp (in yellow) the current clamp reading is set up for 2A.div which with a peak to peak reading of about 3 divisions, suggests a peak current of telling about 3A.

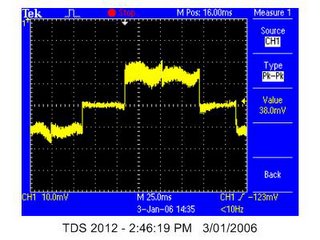
This suggests a standard peak voltage of between 40 and 60mV at 3A. For the IR2175, 260mV is meant to correspond to the peak current. This suggests that there is something wrong. I really should be getting a peak voltage of 26mV.
However if I go back to the calcs for the resistnce of the shunt resistors, I have
R_shuntA = 0.0147 (R_shuntB = 0.0145 and R_shuntC = 0.0142)
This means that the peak current will actually be 17.7A and for 3A the voltage should be 44mV which sounds a lot better.
Now my concern is that I do not understand why the reading from the shunt is in spike s when it should be reading the same current profile as the current clampOne guess is that these spikes are from the PWM switching. It seems that they occur about every 10ms which is 100k so does not really fit in with that theory.
Better check the PWM swithing frequency.the PWM frequency is 7.5kHz - very strange.
checked back at the model and the settings are still set for what I thought was 10k so my change to 20k was not done - strange, better figure that one out.
If i get a PWM frequecy of 7.5k for a PWM period of 10000 then the clock frequency must be 75MHz (or half the DSP clock frequency).
so what is creating the peaks at 100kHz in the voltage accross the shunt?after connecting the scope up again (I have been using a differential measurement ie CH2 - CH1) I have found that I get much better results if I reference both the probes to ground - see image below:
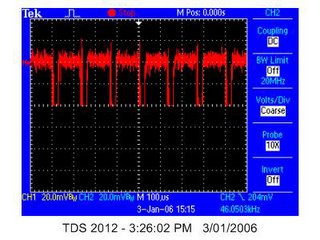
you can clealy see here that 3 of the main wavelengths take up 400us, which corresponds to 7.5k so I have found the PWM frequency.
now if I go back to a longer timebase you can see that I have something that looks pretty similar to the current clamp reading. I assume that the additional noise shown is because of a bandwidth limit on the current clamp.
now it is time to look at the voltage that the IR2175 sees between Vs and V+once again you can see the PWM freqency at 7.5kHz
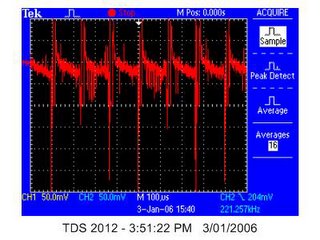
the image at electrical frequency does not look quite as good. It seems that the negative part is not really going negative.

having a look (below) at Vs (blue), V+ (yellow) and the difference there are some strange things going on. The difference is often above 10V which is a bit strange when V+ should be reading only up to 260mV.
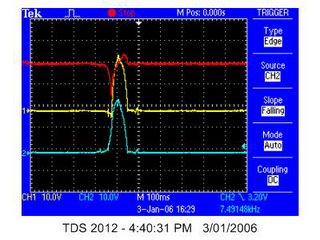
I just checked to see that I am measuring the correct thing and it seems that I am. Pg 3 of the datasheet says that Vin is Vin - Vs.
If I am measuring correctly then the overcurrent trip should be going off regularly - let's see.
you can clearly see that the overcurrent is regularly going off. This should be shutting down the gate driver (need to check that later as there is no obvious indication that this is happening). It seems that the overcurrent is tripping more after the current has stayed constant for a while. My guess at why this is is that when the current is rapidly changing, the impedence due to the inductance is high so less current flows. Once the current is no longer changing rapidly the imedence drops an much more current flows.
It is strange however that the overcurrent signal (which should be a digital signal) is outputting values that are in between 0 and 5V.
Time to check the overcurrent pin without the 2175 in the socket just incase this voltage is coming from elsewhere.
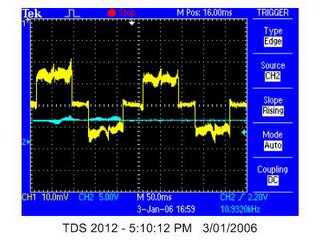
Though there is some noise there, it is definetly not as before, so the overcurrent pin is making a difference.
It is interesting to note that there was no significant difference in motor performance without the chip in. This suggests that the overcurrent pin is not shutting down the gate driver.
As I am stuck for the moment, I will have another go at increasing the PWM frequency. That may also shed light on other issues.I have now fixed this up into a nice masked block.
Interesting that at7.5k the system works for 10% duty cycle but needs a couple of pushes to work at 50% duty cycle, however at 30k the system will not turn no matter how much pushing at 10% and turns fine at 50%. More investigations are due on that matter tomorrow.
Home time.